Containers pile up at rail terminals across the U.S.
under threat of strikes
|
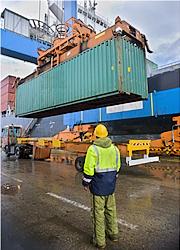 |
Since January 2020, the U.S. rail unions have been in negotiations with the major railroad companies to bargain for a new agreement with pay raises, better healthcare and more staffing. Over the past six years, major railroads have cut their workforce by an average of 29%, and implemented “precision scheduled railroading,” upgrading their networks to run fewer trains on tighter schedules with fewer employees. The unions and railroads entered mediation earlier this year and reached an impasse in June. The next step was a mandatory cooling off period of 30 days, at the end of which either party could have entered into either a strike or lockout. President Biden stepped in at the end of the cooling off period to appoint a Presidential Emergency Board (PEB) to examine the dispute and produce recommendations on a settlement within another 30 days. The PEB’s recommendations are expected by mid-August, after which there will be yet another 30-day cooling off period, during which the parties can either accept or reject those recommendations. If an agreement still has not been reached by mid-September, the Railway Labor Act allows for the unions to go on strike.
Regardless of the threat of a rail strike, the amount of containers sitting in U.S. terminals have been reaching maximum capacity at many inland rail locations. This is (according to carrier CMA), a result of an insufficient supply of both chassis and rail traffic capacity. Containers are piling up at the rail terminals in Chicago, Dallas, Kansas City, Memphis, Denver, St. Louis, Santa Teresa and Omaha. Some railroads such as Union Pacific, have implemented temporary service pauses and train metering to improve capacity issues. The Chamber of Commerce fears that a work stoppage this time could be “disastrous for U.S. consumers and the economy”, and “potentially return to the historic supply chain challenges during the depths of the pandemic.”
For more information, contact Debbie McGuire, Director – Freight Solutions.
ELD enforcement coming January 2023
According to the Canadian Trucking Alliance (CTA), the often-delayed enforcement of Canada’s Electronic Logging Device (ELD) mandate will begin as planned on January 1, 2023. The ELD mandate requires the electronic data collection of truck drivers’ hours of service, similar to the regulation that went into effect in the United States in December of 2017.
While the American and Canadian ELD regulatory requirements are very similar, a big difference is the certification process. In the U.S., the Federal Motor Carrier Safety Administration (FMCSA) allows ELD manufacturers to self-certify their devices to meet regulatory compliance. Canada is requiring third-party certification of devices.
The lack of ELDs certified for use in Canada has been one of the biggest reasons for the delays and the CTA, which represents approximately 4,500 trucking companies in Canada, has voiced concerns that the enforcement of the mandate could be pushed back even further, as ELD providers rush to get certification in place.
As of August 15, 2022, a total of 55 devices were registered and certified according to Transport Canada, a small amount compared to the over 800 devices listed as available for use by the FMCSA in the U.S..
Further raising the prospect of more delays is the fact that four provinces – British Columbia, Quebec, Nova Scotia and Newfoundland – have yet to introduce regulations or legislation required to mandate ELDs. The CTA wants those provinces that have committed to the mandate to proceed with or without the remaining four jurisdictions by the January 2023 enforcement deadline.
“There should be no more moving the goalposts on dates and no more delays. The time to finally start this important safety regime is past due,” CTA president Stephen Laskowski said in a release when the latest delay was announced.
For more information, contact William Sanchez, Manager – Truck Services.
Disruptions have increased awareness of supply chains
Over the last two years, the term supply chain management has gone from one primarily recognized by those within certain jobs to one frequently appearing in news stories. Supply chain disruptions are still regularly discussed by media outlets, and they continue to affect the lives of many – we refer to these as everyday citizens who are outside of the profession but are affected by disruptions, versus those individuals who work inside the supply chain profession to keep the wheels turning or importers/exporters who are also very aware of ongoing disruptions.
This new phenomenon is due to the fact that knowledge of our industry is starting to develop, which is great to hear. While we all notice planes in the air, trucks on the road or intermodal containers moving by train, even basic knowledge of the supply chain industry used to be very limited. Even more so, how disruptions can affect peoples’ day to day lives was relatively unknown, but this changed very quickly. Freight forwarders have dealt with such issues for years, although to a lesser extent than as of late, but managing cargo and dealing with delays is an everyday event. Importers and exporters are also very aware of what is involved in coordinating cargo, and that things do not always go as planned.
The role of freight forwarder goes beyond simply moving freight. Ensuring our clients receive clear and updated information at all times is key, especially during these extremely volatile times in international shipping. It requires us to be in close contact with our clients continually, and in many cases provide guidance and insight on how to best move their cargo, navigating a myriad of ongoing supply chain issues. Keeping partners aware of challenges allows them to address disruptions before they make further impacts down the supply chain. Providing honest updates on supply chain challenges can also build trust with clients, so that they remain loyal after disruptions have subsided.
As noted, the pros in the supply chain field and international shippers have insight into the causes and long term effects of disruptions. This makes them more likely to be greatly concerned about the future of global supply chains. However, as disruptions continue to affect a variety of products and industries connected to the daily lives of everyday citizens, this group has become more concerned about supply chain resiliency in the future.
For more information, contact David Lychek, Director – Ocean & Air Services.
|
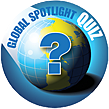 |
|
|
|
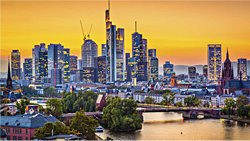 |
|
14 of the country’s tallest skyscrapers
are located in this city. |
Name the city often referred to as ‘Mainhattan’
- Has the suffix ‘am Main’, referring to the river surrounding the city.
- Boasts the largest inner-city forest in the country, featuring a 450 km network of trails.
- Home to the world’s largest book fair.
- Has one of the largest stock exchanges in the world.
- Johann Wolfgang von Goethe was born in this city.
- Home of the inventor of the printing press, Johannes Gutenberg.
- The airport’s baggage system is 67 km long.
See the answer
Answer: Frankfurt, Germany
For more information about shipping freight to or from this city, contact Debbie McGuire, Director – Freight Solutions.
Put delivery and handling instructions in more than one place
Increase your chances of completing a successful delivery of a package by putting handling and delivery instructions on at least three of the surfaces. This simple step will not only lead to fewer stray deliveries, but will also help avoid the damage caused when a package is only marked in one place and it has to be flipped to find the labelling.
|
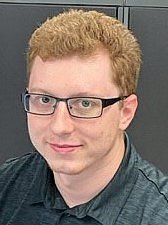 |
|
Cody Keser
Team Leader – Customs Consulting Services (USA) |
At Your Service: Cody Keser, Team Leader – Customs Consulting Services (USA)
Cody Keser joined our US Customs Operations Team in Buffalo in July 2021, where he was responsible for processing customs clearances of import truck shipments, with a goal to take on additional tasks.
In June 2022, Cody was promoted to the role of Team Leader – Customs Consulting Services (USA). Cody is responsible for bringing a variety of compliance activities (HS tariff classification, database maintenance, client consulting, etc.) in-house, in addition to processing claims, protests and duty drawback submissions.
Cody can be reached by phone (716) 882-4100, ext. 2602 or by email. |